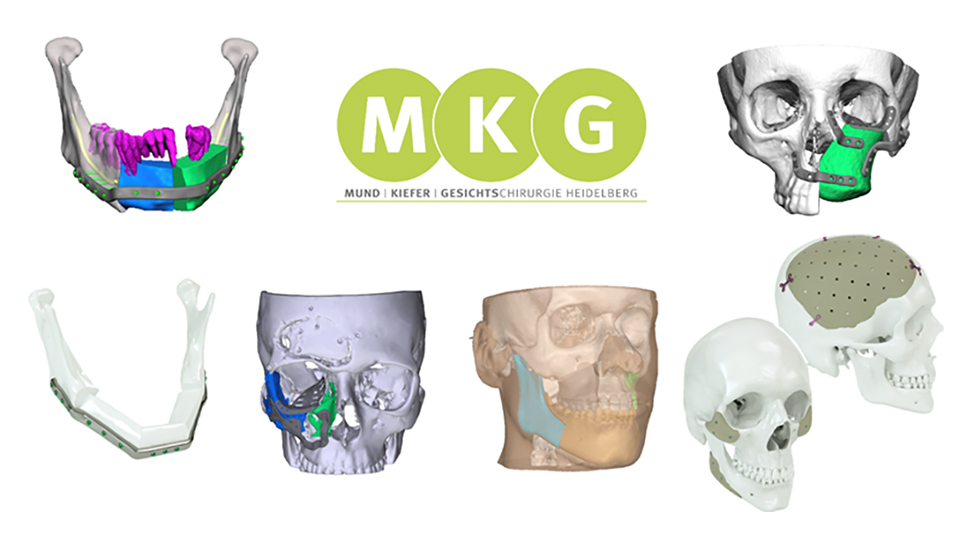
BMBF fördert 3D-Druck von Implantaten
Das Projekt ADDIFEM erhält vom Bundesforschungsministerium eine Förderung in Höhe von 1,2 Mio. Euro. Ziel des Vorhabens: eine schnellere, patientenspezifischere und kostengünstigere Versorgung mit individualisierten 3D-gedruckten Implantaten in der Mund-, Kiefer- und Gesichtschirurgie.
Derzeit ist die Versorgung von Patienten mit komplexen Mittelgesichtsfrakturen sowie im Rahmen der rekonstruktiven, onkologischen und fehlbildungskorrigierenden Chirurgie mit passenden Implantaten kompliziert. Die Planungs- und Herstellungsprozesse für die Implantate dauern sehr lange.
Dieses Problem wird nun am Universitätsklinikum Heidelberg (UKHD) in Angriff genommen, finanziert aus Mitteln des BMBF und des Medizintechnikunternehmens KLS Martin SE & Co. KG. Ziel ist es, die Versorgung der betroffenen Patienten zu beschleunigen. Im Rahmen des Projektes ADDIFEM (Optimierte klinische Point-of-Care-Patientenversorgung durch individualisierte Implantate mittels 3D-Drucktechnologie) wird vor Ort hochmoderne 3D-Drucktechnik installiert. Mit ihr soll dann die Herstellung individualisierter Implantate direkt in der Klinik erfolgen. Am Projekt sind die Arbeitsgruppe um Dr. Reinald Kühle (Oberarzt an der Klinik und Poliklinik für Mund-, Kiefer- und Gerichtschirurgie des UKHD) und als Industriepartner KLS Martin beteiligt.
Projektphase I beinhaltet die Automatisierung und Optimierung der digitalen Planung und des Implantatdesigns. In Phase II sollen dann vor Ort testweise erste Implantate entstehen. Um die Prozesse zu beschleunigen und optimal zu gestalten, ist in der Klinik ein „industrieller Point-of-Care (PoC) vorgesehen. Das heißt, Mitarbeiter des MedTech-Unternehmens KLS Martin werden vor Ort sein. Ziel der aktuellen Machbarkeitsstudie ist es, ein neues, schnelleres Herstellungsverfahren für 3D-Implantate zu etablieren, das im Anschluss auch außerhalb des UKHD zugelassen werden soll.
„Durch die direkte Planung und Herstellung vor Ort erwarten wir neben einer zügigeren Patientenversorgung auch eine höhere Präzision und Passgenauigkeit der individualisierten Implantate und damit eine höhere Erfolgsrate und ein geringeres Komplikationsrisiko“, so Projektleiter Kühle. Das Team rechnet außerdem mit weniger Materialverbrauch. Das neue Herstellungsverfahren wäre damit effizienter und kostengünstiger als herkömmliche Herstellungsmethoden, insbesondere bei der Verwendung teurer Materialien wie PEEK (Polyetheretherketon).
Für die Etablierungsphase erhielt das Team um Kühle zur Durchführung des ersten Teilvorhabens rund 2,2 Mio. Euro – neben den 1,2 Mio. Euro vom BMBF auch rund 1 Mio. Euro vom Industriepartner. Für die drei weiteren Folgeprojekte ist noch eine BMBF-Förderung von bis zu 4,3 Mio. Euro plus Industrieanteile vorgesehen. Die Förderperiode erstreckt sich über insgesamt drei Jahre.