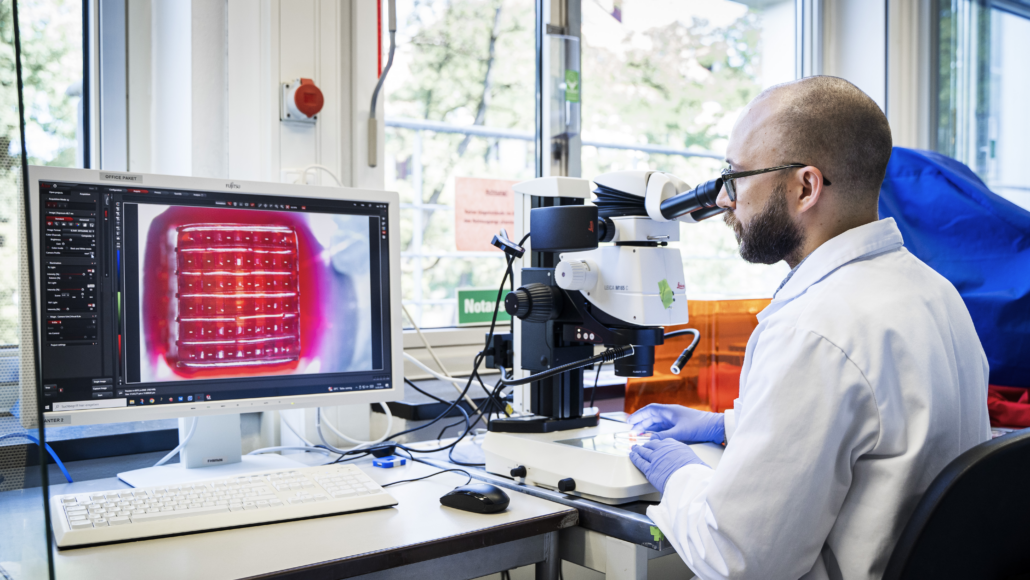
3D-Drucker aus dem Elektromarkt
Wissenschaftler um den Bioingenieur Benedikt Kaufmann vom Centrum für Angewandtes Tissue Engineering und Regenerative Medizin (CANTER) der Hochschule München haben einen handelsüblichen 3D-Drucker für 350 Euro auf 3D-Zelldruck umgerüstet. Die Open-Source-Bauanleitung für das mSLAB getaufte Gerät stellte Kaufmann kostenlos ins Internet.
Das Tissue Engineering wurde als Zukunftstechnologie bereits in mehreren Exzellenzclustern vom BMBF gefördert, und der Organdruck war Gegenstand einer Ausschreibung der Innovationsagentur SPRIND, in deren Rahmen auch zwei Teams aus Deutschland gefördert werden. Nicht umsonst, denn ob 3D-gedruckte Pillen, Gewebe oder Modelle für die Arzneimittelforschung: das wirtschaftliche Potential und die Fortschritte in der Stammzelltechnologie sind groß. Große Durchbrüche wie etwa druckstabilen Knorpel gab es allerdings noch nicht. Ein Grund: Der meist verwendete, weil kostengünstige Extrusions-3D-Druck liefert oft Proteinhydrogele, die wenig formstabil sind und aufgrund des Düsendurchmessers von 100µm bis wenigen Millimetern eine geringe Auflösung zeigen.
Im Gegensatz dazu bietet die Stereolithographie (SLA) eine höhere Druckauflösung und schnellere Verarbeitungsgeschwindigkeiten mit einer breiten Palette von zellfreundlichen Materialien wie Hydrogelen auf Gelatine- oder Kollagenbasis und eignet sich daher gut für die Herstellung von 3D-Gewebekonstruktionen. Entsprechende Drucker kosten mehrere zehntausend Euro und sind daher insbesondere für kleine Forschungslabore schlichtweg unerschwinglich.
Dem hat eine Gruppe um den Bioingenieur Benedikt Kaufmann vom Centrum für Angewandtes Tissue Engineering und Regenerative Medizin (CANTER) der Hochschule München jetzt abgeholfen und einen handelsüblichen 3D-Drucker für 350 Euro, mit dem sich Plastikteile drucken lassen, auf 3D-Zelldruck umgerüstet. Die Open-Source-Bauanleitung für das mSLAB getaufte Gerät stellte Kaufmann kostenlos ins Internet.
„Die größte Herausforderung lag in der Schaffung geeigneter Umgebungsbedingungen,“ erinnert sich Kaufmann: Für die Verarbeitung von Proteinen und Zellen benötigt man neben hoher Luftfeuchtigkeit auch konstant 37° C. Nach ausgiebigen Tests entschieden sich die Bioingenieure für eine effiziente und kostengünstige Lösung: Heizfolien, die sie an das Alugehäuse des Druckers klebten und durch einen Mikrocontroller steuerten. Zudem erzeugt wassergetränkter Zellstoff eine Luftfeuchtigkeit von mehr als 90%. Außerdem ersetzten die Forscher die metallene Druckplatte des Druckers, auf der schichtweise Strukturen aufgebaut werden, durch ein transparentes Glasplättchen, auf das Hydrogele und Zellen direkt aufgedruckt und mikroskopisch untersucht werden können.
Der so umgerüstete Drucker arbeitet mit maskierter Stereolithographie, bei der Licht aus LEDs nach einem programmierten Muster durch ein Flüssigkristall-Display – ähnlich dem eines Handys oder Computer-Monitors – auf das mit einem gelatineartigen Hydrogel benetzte Glasplättchen projiziert wird. Hierbei werden gezielt einzelne Pixel des Displays aktiviert und sorgen so dafür, dass sich die im Hydrogel befindlichen Proteine exakt an den gewünschten Stellen vernetzen und aushärten – Schicht für Schicht entsteht so ein dreidimensionales Gebilde.
Die Ergebnisse, die der Selbstbau in Valdiierungsstudien lieferte, überzeugen laut Kaufmann: „Unsere Versuche haben gezeigt, dass sich mit dem modifizierten 3D-Drucker organische Strukturgerüste mit unterschiedlicher Steifigkeit herstellen lassen – das ist wichtig, weil beispielsweise für Knochensubstanz eine größere Härte erforderlich ist als für Muskelgewebe.“ Die gedruckten Kanäle aus Hydrogelen werden im Tissue Engineering häufig eingesetzt. Mittlerweile ist es der Gruppe auch gelungen, Stammzellen direkt in die Strukturen zu integrieren.
„Ingenieurstechnisches Know-how ist für den Umbau nicht erforderlich,“ betont Kaufmann. Damit sei der Weg auch für kleine Labore frei, das Tissue Engineering weiterzuentwickeln. Selbst in Schulen können mit dem modifizierten Drucker erste Erfahrungen im 3D-Druck von Biomaterialien gesammelt werden.